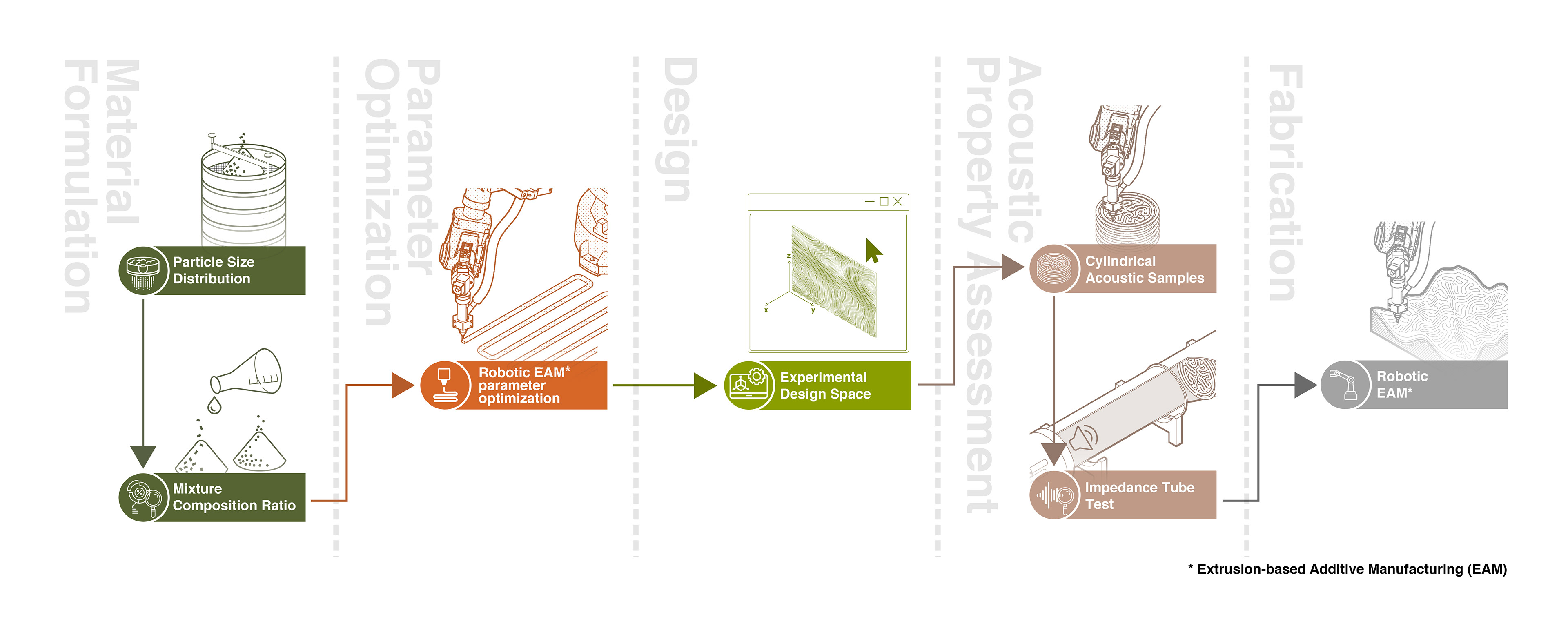
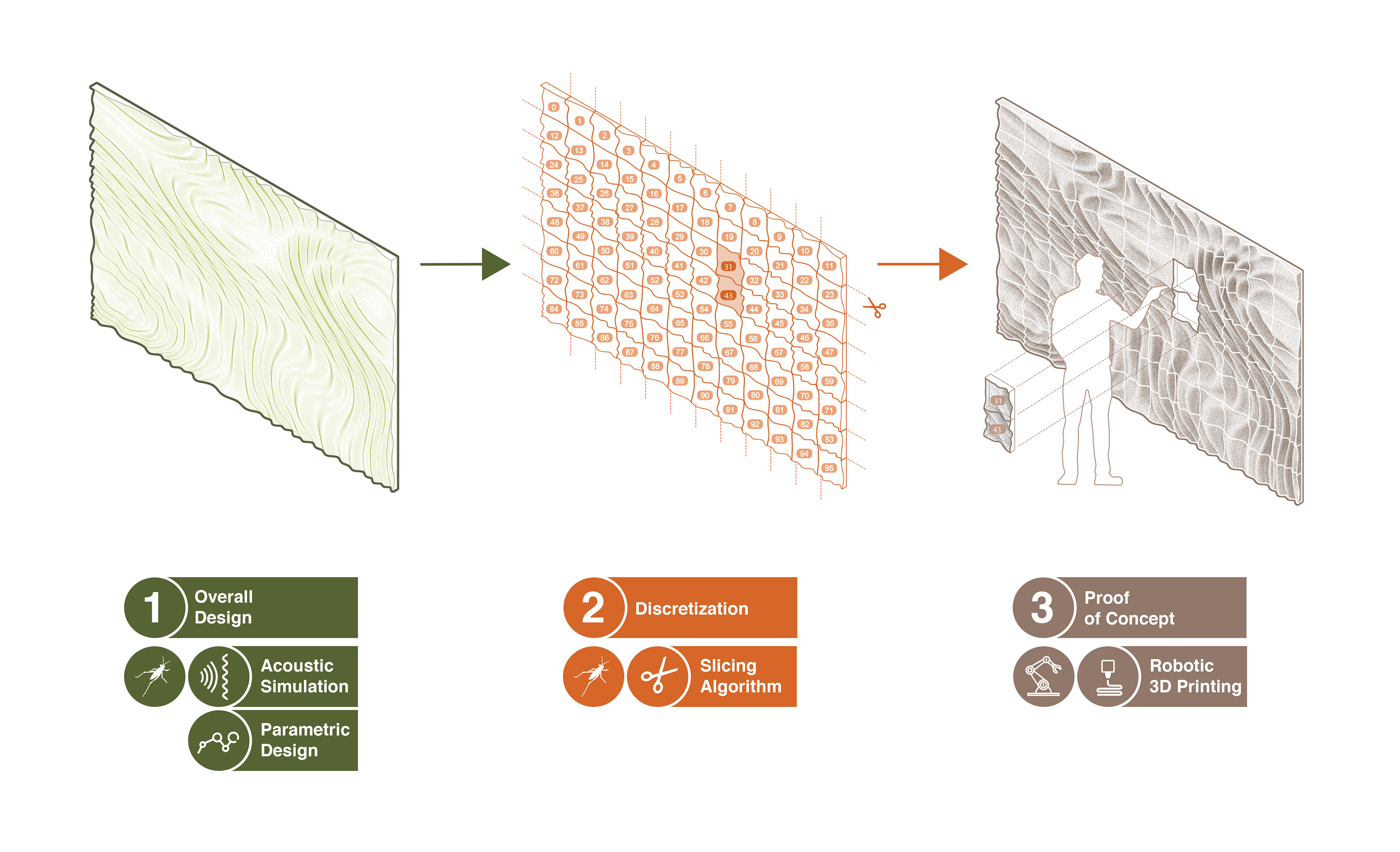
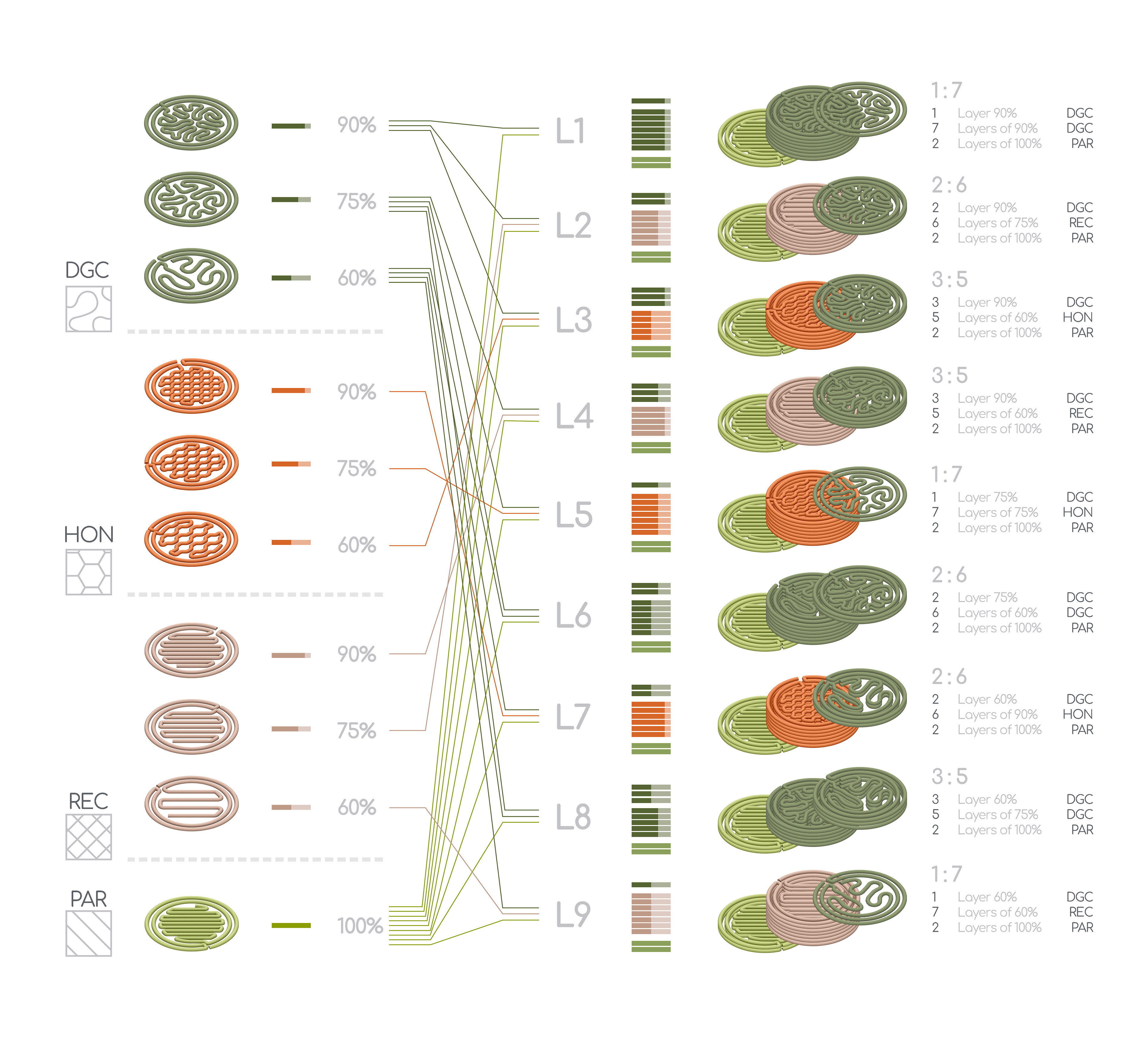
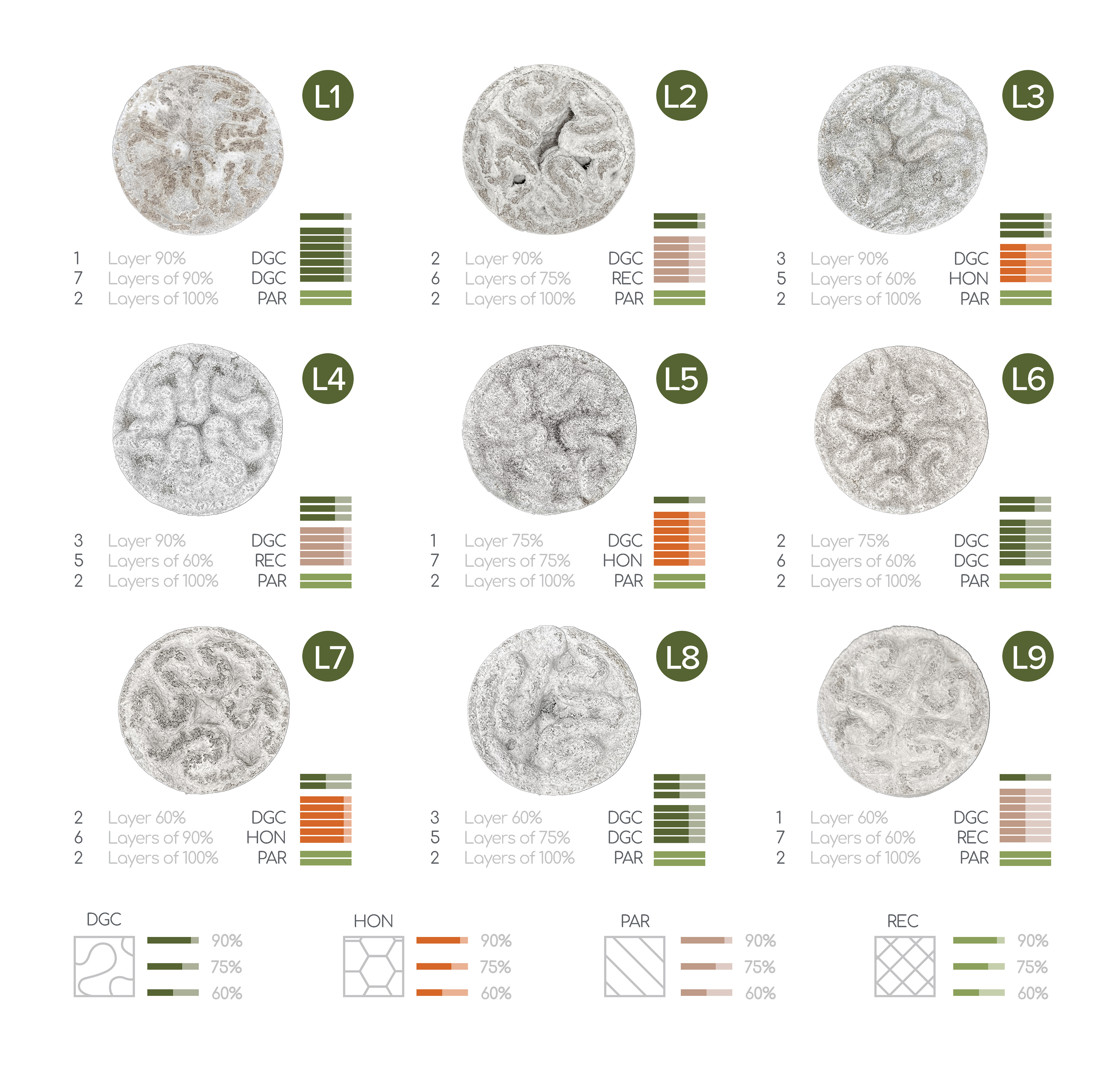
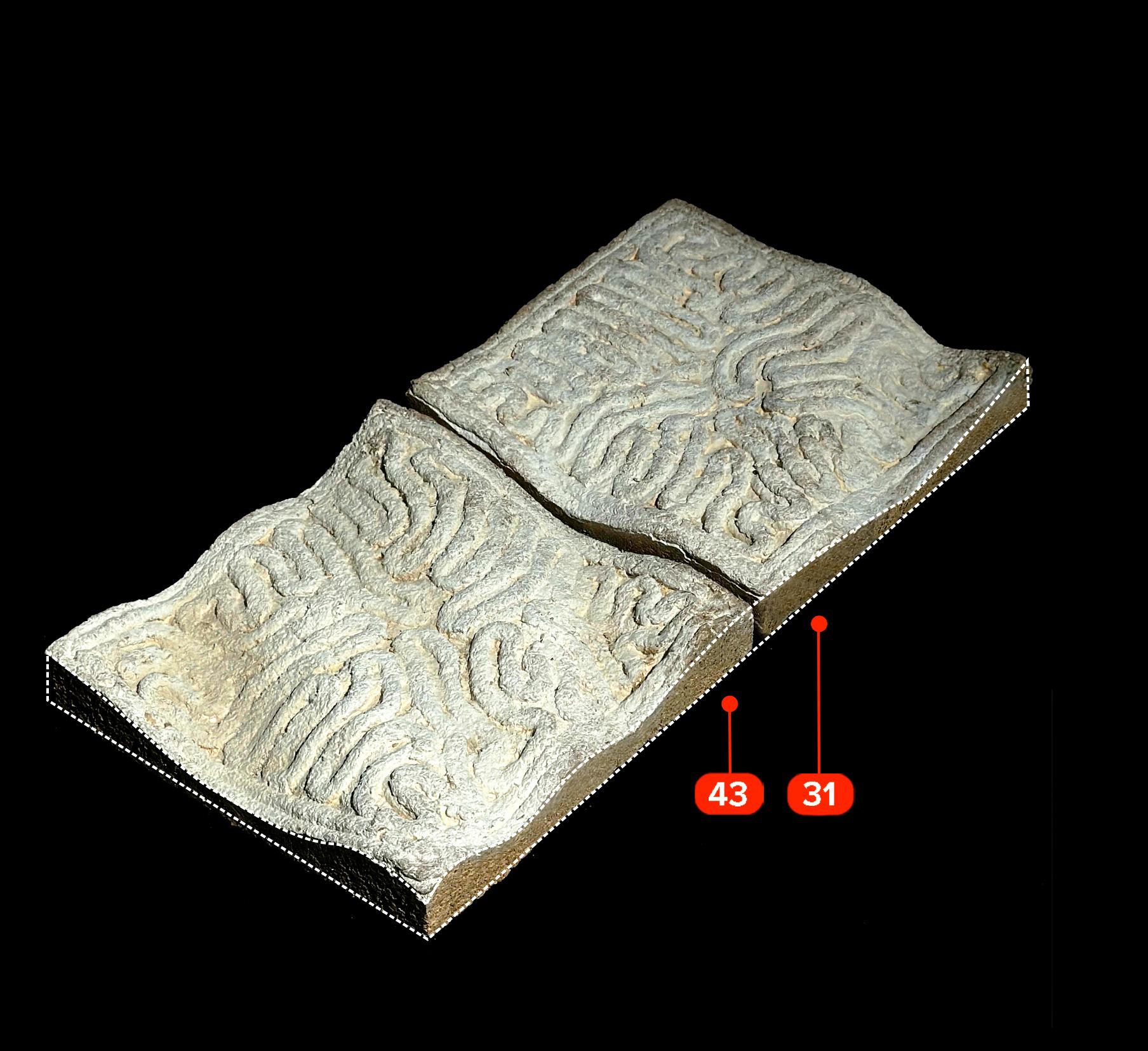
This project presents a data‑driven design and fabrication pipeline to precisely deposit living mycelium composites for sustainable and high-performance acoustic panels by integrating machine learning, design of experiments, and novel robotic workflows. We present an inline inoculation process that reduces total fabrication time from 12 to 7 days. We also introduce a complementary data‑driven deposition model that captures the non‑linear coupling between robot kinematics, extrusion rate, and the rheology of a living substrate. Trained on tens of robotic EAM trials, our custom neural network predicts ideal feed rates and accelerations for an ABB IRB 2400 arm—eliminating manual tuning, slashing physical test iterations, and ensuring uniform bead geometry that underpins consistent acoustic performance. To systematically translate these manufacturing gains into acoustic benefit, we then applied a Taguchi L₉ orthogonal array to explore key toolpath factors: planar vs. non‑planar infill ratios, bead spacing, layer sequencing, and infill patterns (Differential Growth Curve, Parallel, 3D Honeycomb). Impedance‑tube measurements (125–4000 Hz) identified an optimal 60 % non‑planar / 90 % planar infill with a Differential Growth Curve pattern and a 2:6 layer ratio, achieving an average absorption coefficient above 0.20 across the spectrum. A hybrid slicing approach—combining fast, equidistant planar layers with conformal, offset‑surface non‑planar layers—then enables stair‑step–free fabrication of complex geometries at architectural scale, demonstrating a scalable, sustainable route to bespoke, biodegradable acoustic wall panels. Collaborators: Alale Mohseni, Alireza Zamani, Natalie Walter, Benay Gürsoy